În ultimii ani, datorită dezvoltării rapide a noii industrii energetice, sudarea cu laser a pătruns rapid în întreaga nouă industrie energetică datorită avantajelor rapide și stabile. Dintre acestea, echipamentele de sudare cu laser reprezintă cea mai mare proporție de aplicații din întreaga industrie a energiei noi.
Sudarea cu lasera devenit rapid prima alegere în toate domeniile vieții datorită vitezei sale rapide, adâncimii mari și deformării mici. De la suduri prin puncte la suduri cap la cap, suduri de întărire și etanșare,sudare cu laseroferă o precizie și un control de neegalat. Joacă un rol important în producția și producția industrială, inclusiv industria militară, asistența medicală, industria aerospațială, piese auto 3C, tablă mecanică, energie nouă și alte industrii.
În comparație cu alte tehnologii de sudare, sudarea cu laser are avantajele și dezavantajele sale unice.
Avantaj:
1. Viteză mare, adâncime mare și deformare mică.
2. Sudarea se poate executa la temperatura normala sau in conditii speciale, iar echipamentul de sudare este simplu. De exemplu, un fascicul laser nu se deplasează într-un câmp electromagnetic. Laserele pot suda în vid, aer sau anumite medii gazoase și pot suda materiale care sunt prin sticlă sau transparente la fasciculul laser.
3. Poate suda materiale refractare, cum ar fi titanul și cuarțul, și poate suda și materiale diferite cu rezultate bune.
4. După ce laserul este focalizat, densitatea de putere este mare. Raportul de aspect poate ajunge la 5:1 și poate ajunge până la 10:1 la sudarea dispozitivelor de mare putere.
5. Se poate efectua microsudura. După ce fasciculul laser este focalizat, se poate obține un mic punct și poate fi poziționat cu precizie. Poate fi aplicat la asamblarea și sudarea pieselor micro și mici pentru a realiza o producție automată în masă.
6. Poate suda zone greu accesibile și poate efectua sudură pe distanțe lungi fără contact, cu o mare flexibilitate. În special în ultimii ani, tehnologia de procesare cu laser YAG a adoptat tehnologia de transmisie prin fibre optice, ceea ce a permis ca tehnologia de sudare cu laser să fie promovată și aplicată mai pe scară largă.
7. Raza laser este ușor de împărțit în timp și spațiu, iar mai multe fascicule pot fi procesate în mai multe locații simultan, oferind condiții pentru o sudură mai precisă.
Defect:
1. Precizia de asamblare a piesei de prelucrat trebuie să fie ridicată, iar poziția grinzii pe piesa de prelucrat nu poate fi deviată semnificativ. Acest lucru se datorează faptului că dimensiunea spotului laser după focalizare este mică, iar cusătura de sudură este îngustă, ceea ce face dificilă adăugarea de materiale metalice de adaos. Dacă precizia de asamblare a piesei de prelucrat sau precizia de poziționare a grinzii nu îndeplinește cerințele, sunt predispuse să apară defecte de sudare.
2. Costul laserelor și sistemelor conexe este mare, iar investiția unică este mare.
Defecte comune de sudare cu laserîn fabricarea bateriilor cu litiu
1. Porozitatea sudării
Defecte comune însudare cu lasersunt pori. Bazinul topit de sudură este adânc și îngust. În timpul procesului de sudare cu laser, azotul invadează bazinul topit din exterior. În timpul procesului de răcire și solidificare a metalului, solubilitatea azotului scade odată cu scăderea temperaturii. Când metalul topit al piscinei se răcește pentru a începe să cristalizeze, solubilitatea va scădea brusc și brusc. În acest moment, o cantitate mare de gaz va precipita pentru a forma bule. Dacă viteza de plutire a bulelor este mai mică decât viteza de cristalizare a metalului, vor fi generați pori.
În aplicațiile din industria bateriilor cu litiu, descoperim adesea că porii sunt deosebit de probabil să apară în timpul sudării electrodului pozitiv, dar rareori apar în timpul sudării electrodului negativ. Acest lucru se datorează faptului că electrodul pozitiv este din aluminiu, iar electrodul negativ este din cupru. În timpul sudării, aluminiul lichid de la suprafață s-a condensat înainte ca gazul intern să se reverse complet, împiedicând revărsarea gazului și formarea unor găuri mari și mici. Stomatele mici.
În plus față de cauzele porilor menționate mai sus, porii includ și aerul exterior, umiditatea, uleiul de suprafață etc. În plus, direcția și unghiul de suflare a azotului vor afecta, de asemenea, formarea porilor.
Cât despre cum să reduceți apariția porilor de sudare?
În primul rând, înaintesudare, petele de ulei și impuritățile de pe suprafața materialelor primite trebuie curățate la timp; în producția de baterii cu litiu, inspecția materialului primit este un proces esențial.
În al doilea rând, debitul de gaz de protecție trebuie ajustat în funcție de factori precum viteza de sudare, puterea, poziția etc. și nu trebuie să fie nici prea mare, nici prea mic. Presiunea mantalei de protecție trebuie ajustată în funcție de factori precum puterea laserului și poziția de focalizare și nu trebuie să fie nici prea mare, nici prea scăzută. Forma duzei de protecție trebuie să fie ajustată în funcție de forma, direcția și alți factori ai sudurii, astfel încât mantaua de protecție să poată acoperi uniform zona de sudare.
În al treilea rând, controlați temperatura, umiditatea și praful din aerul din atelier. Temperatura și umiditatea mediului ambiant vor afecta conținutul de umiditate de pe suprafața substratului și gazul de protecție, care la rândul lor vor afecta generarea și evacuarea vaporilor de apă în bazinul topit. Dacă temperatura și umiditatea mediului ambiant sunt prea mari, va exista prea multă umiditate pe suprafața substratului și a gazului protector, generând o cantitate mare de vapori de apă, rezultând pori. Dacă temperatura și umiditatea mediului ambiant sunt prea scăzute, va exista prea puțină umiditate pe suprafața substratului și în gazul de protecție, reducând generarea de vapori de apă, reducând astfel porii; lăsați personalul de calitate să detecteze valoarea țintă a temperaturii, umidității și prafului la stația de sudare.
În al patrulea rând, metoda de balansare a fasciculului este utilizată pentru a reduce sau elimina porii în sudarea cu penetrare adâncă cu laser. Datorită adăugării de oscilație în timpul sudării, oscilația alternativă a grinzii la cordonul de sudură determină retopirea repetată a unei părți a cordonului de sudură, ceea ce prelungește timpul de rezidență al metalului lichid în bazinul de sudură. În același timp, deviația fasciculului crește și aportul de căldură pe unitate de suprafață. Raportul adâncime-lățime al sudurii este redus, ceea ce favorizează apariția bulelor, eliminând astfel porii. Pe de altă parte, oscilația fasciculului face ca gaura mică să se balanseze în consecință, ceea ce poate oferi, de asemenea, o forță de agitare pentru bazinul de sudură, poate crește convecția și agitarea bazinului de sudură și poate avea un efect benefic asupra eliminării porilor.
În al cincilea rând, frecvența pulsului, frecvența pulsului se referă la numărul de impulsuri emise de raza laser pe unitatea de timp, care va afecta intrarea de căldură și acumularea de căldură în bazinul topit și apoi va afecta câmpul de temperatură și câmpul de curgere în topitul. piscină. Dacă frecvența pulsului este prea mare, va duce la un aport excesiv de căldură în bazinul topit, determinând temperatura prea ridicată a bazinului topit, producând vapori de metal sau alte elemente care sunt volatile la temperaturi ridicate, rezultând pori. Dacă frecvența pulsului este prea scăzută, aceasta va duce la o acumulare insuficientă de căldură în bazinul topit, ceea ce face ca temperatura bazinului topit să fie prea scăzută, reducând dizolvarea și scăparea gazului, rezultând pori. În general, frecvența pulsului ar trebui să fie aleasă într-un interval rezonabil bazat pe grosimea substratului și puterea laserului și să evite să fie prea mare sau prea scăzută.
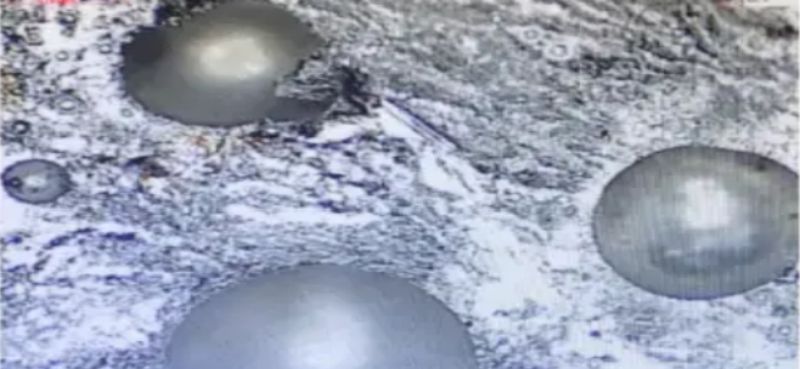
Găuri de sudare (sudare cu laser)
2. Stropi de sudură
Stropirea generată în timpul procesului de sudare, sudarea cu laser va afecta grav calitatea suprafeței sudurii și va polua și deteriora lentila. Performanța generală este următoarea: după terminarea sudării cu laser, multe particule de metal apar pe suprafața materialului sau a piesei de prelucrat și aderă la suprafața materialului sau a piesei de prelucrat. Cea mai intuitivă performanță este că la sudarea în modul galvanometru, după o perioadă de utilizare a lentilei de protecție a galvanometrului, vor exista gropi dense la suprafață, iar aceste gropi sunt cauzate de stropii de sudură. După mult timp, este ușor să blocați lumina și vor apărea probleme cu lumina de sudură, rezultând o serie de probleme, cum ar fi sudarea ruptă și sudarea virtuală.
Care sunt cauzele stropirii?
În primul rând, densitatea de putere, cu cât densitatea de putere este mai mare, cu atât este mai ușor să generați stropi, iar stropirea este direct legată de densitatea de putere. Aceasta este o problemă veche de un secol. Cel puțin până acum, industria nu a reușit să rezolve problema stropirii și nu poate decât să spună că aceasta a fost ușor redusă. În industria bateriilor cu litiu, stropirea este cel mai mare vinovat al scurtcircuitului bateriei, dar nu a reușit să rezolve cauza principală. Impactul stropilor asupra bateriei poate fi redus doar din punct de vedere al protecției. De exemplu, un cerc de porturi de îndepărtare a prafului și capace de protecție sunt adăugate în jurul părții de sudură, iar rânduri de cuțite de aer sunt adăugate în cercuri pentru a preveni impactul stropilor sau chiar deteriorarea bateriei. Distrugerea mediului, produselor și componentelor din jurul stației de sudură se poate spune că a epuizat mijloacele.
În ceea ce privește rezolvarea problemei stropilor, se poate spune doar că reducerea energiei de sudare ajută la reducerea stropilor. Reducerea vitezei de sudare poate ajuta, de asemenea, dacă penetrarea este insuficientă. Dar în unele cerințe speciale de proces, are un efect redus. Este același proces, mașini diferite și loturi diferite de materiale au efecte de sudare complet diferite. Prin urmare, există o regulă nescrisă în noua industrie a energiei, un set de parametri de sudare pentru o singură piesă de echipament.
În al doilea rând, dacă suprafața materialului prelucrat sau a piesei de prelucrat nu este curățată, petele de ulei sau poluanții vor provoca, de asemenea, stropi serioase. În acest moment, cel mai ușor este să curățați suprafața materialului prelucrat.
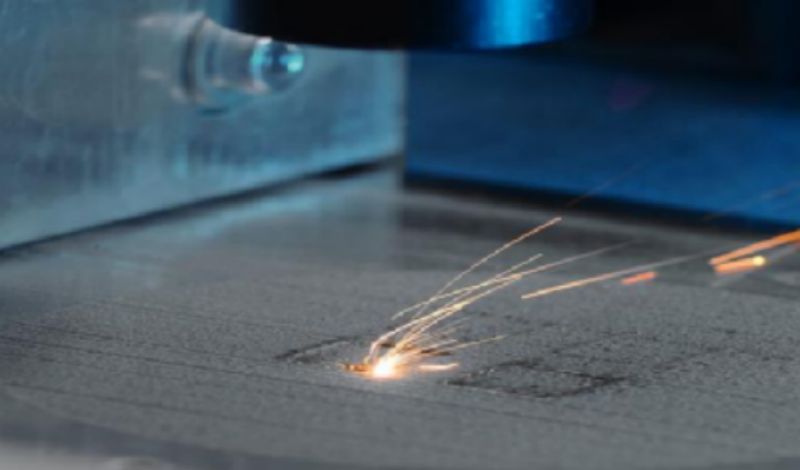
3. Reflexivitate ridicată a sudării cu laser
În general, reflexia ridicată se referă la faptul că materialul de prelucrare are o rezistivitate mică, o suprafață relativ netedă și o rată de absorbție scăzută pentru laserele cu infraroșu apropiat, ceea ce duce la o cantitate mare de emisie laser și pentru că majoritatea laserelor sunt utilizate. în verticală Datorită materialului sau a unei mici înclinații, lumina laser care se întoarce reintră în capul de ieșire și chiar și o parte din lumina care se întoarce este cuplată în fibra de transmitere a energiei și este transmisă înapoi de-a lungul fibrei către interior. a laserului, ceea ce face ca componentele centrale din interiorul laserului să continue să fie la temperatură ridicată.
Când reflectivitatea este prea mare în timpul sudării cu laser, pot fi luate următoarele soluții:
3.1 Utilizați un strat anti-reflex sau tratați suprafața materialului: acoperirea suprafeței materialului de sudură cu un strat anti-reflex poate reduce în mod eficient reflectivitatea laserului. Această acoperire este de obicei un material optic special cu reflectivitate scăzută care absoarbe energia laserului în loc să o reflecte înapoi. În unele procese, cum ar fi sudarea colectorului de curent, conexiunea soft etc., suprafața poate fi, de asemenea, gofrată.
3.2 Reglarea unghiului de sudare: Prin ajustarea unghiului de sudare, fasciculul laser poate incide pe materialul de sudare la un unghi mai adecvat și poate reduce apariția reflexiei. În mod normal, a avea fasciculul laser incident perpendicular pe suprafața materialului de sudat este o modalitate bună de a reduce reflexiile.
3.3 Adăugarea de absorbant auxiliar: în timpul procesului de sudare, o anumită cantitate de absorbant auxiliar, cum ar fi pulbere sau lichid, este adăugată la sudare. Aceste absorbante absorb energia laserului și reduc reflectivitatea. Absorbantul adecvat trebuie selectat pe baza materialelor de sudare specifice și a scenariilor de aplicare. În industria bateriilor cu litiu, acest lucru este puțin probabil.
3.4 Utilizați fibră optică pentru a transmite laserul: Dacă este posibil, fibra optică poate fi folosită pentru a transmite laserul în poziția de sudare pentru a reduce reflectivitatea. Fibrele optice pot ghida fasciculul laser către zona de sudare pentru a evita expunerea directă la suprafața materialului de sudură și pentru a reduce apariția reflexiilor.
3.5 Ajustarea parametrilor laser: Prin ajustarea parametrilor precum puterea laserului, distanța focală și diametrul focal, distribuția energiei laser poate fi controlată și reflexiile pot fi reduse. Pentru unele materiale reflectorizante, reducerea puterii laserului poate fi o modalitate eficientă de a reduce reflexiile.
3.6 Utilizați un divizor de fascicul: Un divizor de fascicul poate ghida o parte din energia laser în dispozitivul de absorbție, reducând astfel apariția reflexiilor. Dispozitivele de separare a fasciculului constau de obicei din componente optice și absorbante, iar prin selectarea componentelor adecvate și ajustarea aspectului dispozitivului, se poate obține o reflectivitate mai mică.
4. Decupaj de sudare
În procesul de fabricare a bateriilor cu litiu, ce procese sunt mai susceptibile de a provoca subcotare? De ce apare subcotarea? Să o analizăm.
Undercut, în general, materiile prime de sudură nu sunt bine combinate între ele, golul este prea mare sau apare canelura, adâncimea și lățimea sunt practic mai mari de 0,5 mm, lungimea totală este mai mare de 10% din lungimea sudurii sau mai mare decât standardul de proces al produsului lungimea cerută.
În întregul proces de fabricare a bateriilor cu litiu, este mai probabil să apară subcotarea și este, în general, distribuită în presudarea și sudarea de etanșare a plăcii de acoperire cilindrice și în presudarea și sudarea de etanșare a plăcii de acoperire a carcasei pătrate din aluminiu. Motivul principal este că placa de acoperire de etanșare trebuie să coopereze cu carcasa la sudare, procesul de potrivire dintre placa de acoperire de etanșare și carcasă este predispus la goluri excesive de sudură, caneluri, colaps etc., deci este deosebit de predispus la decupări. .
Deci, ce cauzează subcotarea?
Dacă viteza de sudare este prea mare, metalul lichid din spatele găurii mici îndreptate către centrul sudurii nu va avea timp să se redistribuie, rezultând solidificare și subtăiere pe ambele părți ale sudurii. Având în vedere situația de mai sus, trebuie să optimizăm parametrii de sudare. Pentru a spune simplu, este vorba de experimente repetate pentru a verifica diferiți parametri și continuați să faceți DOE până când sunt găsiți parametrii corespunzători.
2. Golurile excesive de sudură, canelurile, prăbușirile etc. ale materialelor de sudură vor reduce cantitatea de metal topit care umple golurile, făcând mai probabil să apară subtăieri. Aceasta este o chestiune de echipamente și materii prime. Dacă materiile prime de sudură îndeplinesc cerințele de material primite ale procesului nostru, dacă precizia echipamentului îndeplinește cerințele etc. Practica normală este de a tortura și de a bate în mod constant furnizorii și persoanele responsabile cu echipamentul.
3. Dacă energia scade prea repede la sfârșitul sudării cu laser, orificiul mic se poate prăbuși, ducând la subtăierea locală. Potrivirea corectă a puterii și vitezei poate preveni în mod eficient formarea de tăieturi. După cum spune vechea zicală, repetați experimentele, verificați diferiți parametri și continuați DOE până când găsiți parametrii potriviți.
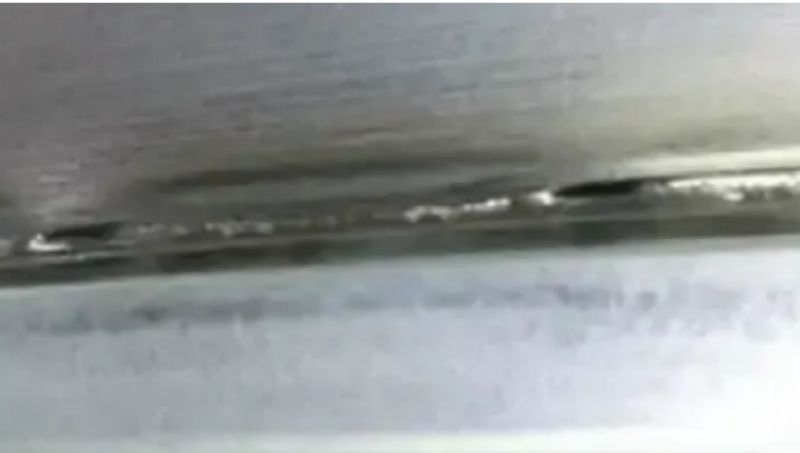
5. Colapsul centrului de sudare
Dacă viteza de sudare este mică, bazinul topit va fi mai mare și mai larg, crescând cantitatea de metal topit. Acest lucru poate face dificilă menținerea tensiunii superficiale. Când metalul topit devine prea greu, centrul sudurii se poate scufunda și poate forma gropi și gropi. În acest caz, densitatea de energie trebuie redusă în mod corespunzător pentru a preveni prăbușirea bazinului de topire.
Într-o altă situație, golul de sudură formează doar o prăbușire fără a provoca perforații. Aceasta este, fără îndoială, o problemă de ajustare prin presare a echipamentelor.
O înțelegere adecvată a defectelor care pot apărea în timpul sudării cu laser și a cauzelor diferitelor defecte permite o abordare mai direcționată pentru a rezolva orice probleme anormale de sudare.
6. Fisuri de sudare
Fisurile care apar în timpul sudării continue cu laser sunt în principal fisuri termice, cum ar fi fisurile de cristal și fisurile de lichefiere. Cauza principală a acestor fisuri este forțele mari de contracție generate de sudare înainte ca aceasta să se solidifice complet.
Există, de asemenea, următoarele motive pentru fisuri în sudarea cu laser:
1. Proiectare nerezonabilă a sudurii: Proiectarea necorespunzătoare a geometriei și dimensiunii sudurii poate cauza concentrarea tensiunilor de sudare, provocând astfel fisuri. Soluția este optimizarea designului sudurii pentru a evita concentrarea tensiunilor de sudare. Puteți utiliza suduri offset corespunzătoare, puteți schimba forma sudurii etc.
2. Nepotrivirea parametrilor de sudare: Selectarea necorespunzătoare a parametrilor de sudare, cum ar fi viteza de sudare prea mare, puterea prea mare etc., poate duce la schimbări neuniforme ale temperaturii în zona de sudare, ducând la stres mari de sudare și fisuri. Soluția este ajustarea parametrilor de sudare pentru a se potrivi cu materialul specific și condițiile de sudare.
3. Pregătirea slabă a suprafeței de sudură: Necurățarea și pre-tratarea adecvată a suprafeței de sudare înainte de sudare, cum ar fi îndepărtarea oxizilor, grăsimii etc., va afecta calitatea și rezistența sudurii și va duce cu ușurință la fisuri. Soluția este să curățați și să pre-tratați în mod adecvat suprafața de sudură pentru a vă asigura că impuritățile și contaminanții din zona de sudare sunt tratate eficient.
4. Control necorespunzător al aportului de căldură de sudare: Controlul slab al aportului de căldură în timpul sudării, cum ar fi temperatura excesivă în timpul sudării, viteza de răcire necorespunzătoare a stratului de sudură etc., va duce la modificări în structura zonei de sudare, ducând la fisuri . Soluția este de a controla temperatura și viteza de răcire în timpul sudării pentru a evita supraîncălzirea și răcirea rapidă.
5. Reducere insuficientă a tensiunii: Tratamentul insuficient de reducere a tensiunii după sudare va duce la o reducere suficientă a tensiunii în zona sudată, ceea ce va duce cu ușurință la fisuri. Soluția este efectuarea unui tratament adecvat de reducere a tensiunilor după sudare, cum ar fi tratamentul termic sau tratamentul vibrațiilor (motivul principal).
În ceea ce privește procesul de fabricație a bateriilor cu litiu, ce procese sunt mai susceptibile de a provoca fisuri?
În general, fisurile sunt predispuse să apară în timpul sudării de etanșare, cum ar fi sudarea de etanșare a carcaselor cilindrice de oțel sau a carcasei de aluminiu, sudarea de etanșare a carcasei pătrate de aluminiu etc. În plus, în timpul procesului de ambalare a modulului, sudarea colectorului de curent este, de asemenea, predispusă. la fisuri.
Desigur, putem folosi și sârmă de umplutură, preîncălzire sau alte metode pentru a reduce sau elimina aceste fisuri.
Ora postării: 01-sept-2023